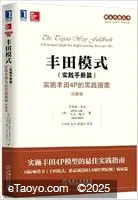
编辑推荐
《丰田模式(实践手册篇):实施丰田4P的实践指南(珍藏版)》由机械工业出版社出版。《丰田模式(实践手册篇):实施丰田4P的实践指南(珍藏版)》为你提供了多种分析工具、工作表和练习——其中许多改编自丰田的真实文件——以便你可以为你的公司制定最有效的方法。更为重要的是,你可以理解精益工具和方法背后所蕴含的思维方式,从而将丰田的4P模型全面而永久地融入你的组织之中。
作者简介
作者简介杰弗瑞·莱克现任密歇根大学工业与运营工程系教授,并担任该校日本技术管理项目主任。代表作包括《丰田模式:精益制造的14项管理原则》(由麦格劳-希尔公司于2004年出版,该书曾荣获2005年“新乡奖”、美国工业工程协会2005年度图书等殊荣)。他所编著的《迈向精益》(Becoming Lean)因对制造业提出精辟研究而赢得1998年“新乡奖”。此外,他也凭借的研究贡献分别在1995年、1996年和1997年赢得“新乡奖”。莱克的其他著作包括Engineered in Japan、Concurrent Engineering Effectiveness、Remade in America,以及与詹姆斯·摩根(James Morgan)合著的《高性能产品开发》(High Performance Product Development)。莱克经常应邀为企业主管举办讲座,并以个人名义或与他人共同创办的管理顾问公司Optiprise Inc.首席顾问的身份担任精益顾问,近期客户包括戴姆勒-克莱斯勒、麦塔尔萨、丹佛斯、力拓矿业、卡特彼勒亚太区分公司、本特勒汽车、法马通公司、诺斯罗普·格鲁门公司舰船系统部、杰克逊维尔海空维修基地、美国空军、朴次茅斯海军船厂等。
大卫·梅尔曾作为丰田肯塔基州乔治城工厂塑料铸模部聘任的第一批团队领导人之一进行丰田生产方式的学习。他先后在日本和肯塔基州接受丰田生产方式专家长达十年的培训和指导,其中包括多名协调员负责的全职培训。离开丰田之后,他创建了美国精益顾问公司(Lean Associates),致力于为追求实行丰田生产方式的企业提供支持服务。
大卫为《精益制造:车间现场指南》(Lean Manufacturing: A Plant Floor Guide)一书撰写了两章内容,并担任培训师长达8年。梅尔曾举办标准化作业、绘制价值流图、制造工程师协会精益基础入门、“新乡奖”研讨会等培训讲习班。他曾为各行各业的公司提供咨询与指导,涉及领域包括汽车、航空航天、木材和塑料产品加工、化学产品加工、金属加工、制造生产、焊接及制造业和非制造业的装配作业等。梅尔擅长在组织内部实行丰田生产方式,使组织实现精益转型。
目录
推荐序
作者简介
前言
致谢
第一篇向丰田学习
第1章实践指南的背景 2
为何撰写本书 2
本书的篇章结构 5
丰田模式原则综述 7
如何使用本书 13
第二篇你的公司为何存在
第2章明确公司目的并开始践行 16
你公司的理念是什么 16
内部和外部的目的感 17
创建你的理念 22
践行你的理念 24
与员工和合作伙伴签订社会契约 25
保持目的的连续性 26
第三篇在整个企业中创建精益流程
第3章开启减少浪费之旅 30
精益就是杜绝浪费 30
建立减少浪费的长期理念 34
价值流图法 35
价值流图法的益处 38
绘制现状价值流图 39
绘制现状价值流图时必须了解你的目标 39
价值流图法的局限性 44
按部就班地创建无间断流程 44
相继的与同步的持续改进 48
第4章创建初步的流程稳定性 52
首先实现基本的稳定性 52
不稳定的指标 53
拨云见日 54
稳定性的目标 55
实现稳定性的策略 56
识别并消除大浪费 56
站在圆圈内的练习 57
以标准化作业作为识别和消除浪费的工具 57
5S和工作场所组织 60
整合浪费活动,以获取收益 61
改进运行效率 66
通过隔离法减少变异 68
均衡工作量,为创建无间断流程和标准化奠定基础 72
第5章创建无间断流程 74
单件流是理想 74
为何要创建无间断流程 76
少即多:控制生产过剩,减少浪费 77
创建无间断流程的策略 83
单件流 83
实现无间断流程的主要标准 84
拉动式制度 87
复杂的单件流 91
定制制造业的拉动式制度 92
在独立的作业步骤之间创建拉动 95
无间断流程、拉动式制度和杜绝浪费 100
第6章建立标准化流程与程序 104
标准化是强制性的吗 104
标准化作业抑或是作业标准 106
标准化的目标 107
建立标准化流程和程序的策略 109
标准化的类型 110
质量、安全与环境标准 112
标准规范 113
标准程序 114
对标准化作业的误解 114
标准化作业 117
标准化作业文件 118
制定标准化作业面临的挑战 123
标准化作业的审核 125
以标准化作业作为持续改善的基线 127
以生产节拍作为设计参数 128
可视化控制的重要性 130
标准化作业是一种消除浪费的工具 133
第7章均衡化:向乌龟学习,不要像兔子 136
均衡化的矛盾 136
均衡化为资源规划提供了标准化的核心 137
为什么迫使自己实行均衡化 138
平稳上游流程的需求 139
如何制定基本均衡化的生产计划表 142
渐进式均衡化和高级均衡化 147
渐进式均衡化 148
控制点 148
存货管理的控制点 149
均衡化的生产计划表决定补货作业 150
产品种类繁多时的“切片切块”多维分析法 151
均衡化需要全企业的共同努力 156
第8章建立一种暂停作业以解决问题的文化 160
形成文化 161
自动化的作用:自我监控的机器 165
解决问题的循环 167
将生产线暂停时间降至最低 171
将质量检查内建于每一项工作之中 173
差错预防技术 174
创建支持架构 183
第9章使技术与员工和精益流程相匹配 186
倒退到算盘时代 186
你如何看待技术、员工与流程 188
调整技术以适应你的员工和经营理念 191
对比不同的技术采纳模型 193
正确地运用技术 200
第四篇培养杰出的员工和合作伙伴
第10章培养彻底了解公司体系的领导者 206
成功始于领导能力 206
丰田公司领导能力的重要意义 207
丰田公司乔治城工厂生产线的领导结构 209
丰田公司乔治城工厂参谋领导结构 211
领导者的必备条件 211
一个典型工作日中团队领导人的职责 213
创建生产领导结构 219
领导干部的选拔 220
培养领导者 224
领导者的接替计划 225
第11章培养杰出的团队成员 228
我们不只制造汽车,也在塑造人 228
从选拔正确的员工开始 229
让团队成员融入你的公司文化 232
工作指导培训:培养杰出技能水平的关键 234
制定培训计划,追踪工作表现 241
立足长远利益培养团队成员 244
质量圈 245
丰田的建议体系 247
培养团队成员承担领导角色 249
联谊活动增强团队凝聚力 251
投资发展公司各个领域的技能 251
第12章将供应商和合作伙伴发展为企业的外延 256
在全球竞争环境中的供应商伙伴 256
短期的节约成本与长期的伙伴关系 257
丰田模式下的供应商伙伴 259
供应商伙伴关系的七个特点 261
建立精益的扩展企业 277
供应商管理的传统模式与精益模式对比 281
第五篇从根本上解决问题,实现持续学习
第13章丰田模式解决问题的方法 292
不只是解决问题 292
每个问题都是改善的机会 294
讲述解决问题的故事 297
第14章彻底了解情况并定义问题 307
认真瞄准后再开枪 307
找出真正的问题,获得最显著的成效 311
反方向考察问题 317
定义问题 317
建立强大的支持依据 320
第15章进行彻底的根本原因分析 324
有效分析的原则 324
探索可解决的问题原因 329
将根本原因分析提炼成最简单形式 331
一幅图胜过千言万语 332
全部集中汇总:一页A3纸报告 333
深入发掘可能的原因 335
第16章考虑各种可行的解决方案,建立共识 337
广泛考虑各种可能性 337
评估的简单性、成本、控制范围和快速实施能力 339
建立共识 340
测试想法的有效性 341
选择最佳的解决方案 342
正确定义问题,解决方法则水到渠成 342
第17章计划—实施—检查—处理 344
计划:制定行动计划 345
实施:实施解决方案 348
检查:检验成果 348
处理:对解决方案和行动计划做出必要调整 350
处理:确定未来步骤 351
最终实施行动 352
第18章使用A3纸报告来说明情况 355
撰写报告时,简单的形式可能带来更好的效果 355
确定如何使用A3纸报告 356
解决问题A3纸报告流程 358
A3纸报告概述 360
版式设计建议 361
解决问题情况的A3纸报告最终版 363
A3纸报告的最后评论 366
第六篇管理变革
第19章实施精益解决方案的策略与方法 370
从哪里入手 370
精益的执行层级、策略和工具 371
耐心去做 394
第20章领导变革 403
我们能避免精益变革中涉及的政治因素吗 403
高层、中层与基层的领导 406
能否靠评估指标来实现精益 424
改变行为以改变文化 430
把你的学习推广至事业伙伴 434
现在请尝试并全力以赴 437
译后记 442
序言
推荐序当杰弗瑞·莱克和大卫·梅尔让我为这本实践指南作序时,我立刻热情地答应了下来,但旋即又有些许担心。一本关于丰田模式的“实践指南”?到底什么是实践指南,又该如何来形容丰田模式?像一本提供各种食谱的烹饪书籍,还是一本路线图?但是通过阅读本书,读者会发现这根本不是什么烹饪书籍或路线图,而是一个能够指明方向的指南针,它能够帮助你找到属于自己的道路。而作者杰弗瑞和大卫则是你的领路人,他们装备齐全,定能为你提供莫大的帮助,我对此深信不疑。碰巧的是,当杰弗瑞和大卫首次参加在丰田市举办的全球高级工商管理项目时,我都在场,只不过与他们每个人见面的场景不同而已。和杰弗瑞见面的时候,我当时还在丰田工作,而他则是密歇根大学的一名教授,正在进行社会技术体系方面的研究,其实,早在他还是马萨诸塞大学的一名学生时,他就已经开始了这项研究。与大卫·梅尔的碰面则是在我向丰田在美国的新员工介绍丰田生产方式的时候。当时,他正在车间现场学习丰田模式——或许,你也应该像他一样,到车间现场去学习。
杰弗瑞与丰田的结缘源自正规教育和后续的研究,他对工业的“软科学”与“硬科学”拥有同样的兴趣和经验。作为一名工业工程师和东北大学(美国)带薪实习的学生,杰弗瑞在通用食品公司(General Foods Corporation)工作,负责运营研究、工厂布局等工业工程工作,然而最令他感兴趣的却是一家位于托皮卡的狗粮工厂。这家工厂依据社会技术体系——社会与技术系统联合设计而成,围绕实行自我管理的不同团队组织创建。在马萨诸塞大学获得博士学位之后,杰弗瑞加入了这所大学的工业与运营工程学院,并一直在那里任教至今。通过和大卫·科尔(David Cole)、罗伯特·科尔(Robert Cole)等人一起参加著名的密歇根大学美日汽车研究项目,杰弗瑞对汽车行业和日本的研究进一步深入发展,并进而接触到丰田及丰田生产方式。在丰田,他发现自己研究多年的社会科技体系得到了实际应用。也正是在这里,他认为他终于找到了一个将社会和科技体系实现真正融合的组织。
杰弗瑞与政治学教授约翰·坎贝尔(John Campbell)及密歇根商学院的布莱恩·塔尔伯特(Brian Talbot)教授共同创建了日本技术管理项目(我曾经有幸为其工作多年),旨在研究日本的成功组织如何进行技术管理。他们在研究过程中认识到,众多日本企业在各自领域内的竞争优势并非源自“硬”技术(比如,丰田所使用的锻压机和机器人与福特所使用的锻压机和机器人源自同一家供应商),关键在于对相同技术的管理方式。因此,这个项目重点关注的是一些企业(尤其是丰田)将技术与人、机构、产品和策略实现整体融合的方式。经研究发现,这些企业的与众不同之处在于它们的社会科技体系,尽管很少有企业会用这样的术语来解释这个问题。
大卫的实地学习机会从工厂现场开始。1987年夏天,他成为丰田肯塔基工厂(TMMK)第一批派往丰田市的一线监管员团队中的一员,前往丰田接受管理培训。那时,丰田已经“实践”过了以合资形式创建的新联合汽车制造有限公司(NUMMI),而乔治城是丰田在日本境外第一家实现完全自主经营的工厂。与肯塔基州政府合作,丰田开发了一套全面的评估方案来选拔应聘首批3 000个工作岗位的10万名应征者!而大卫是在首轮选拔中便脱颖而出的基层领导人员之一。此次选拔过程异常严格,但这只是整个培训开发流程的序曲,在接下来的几年里,大卫又接受了更多紧张而充实的培训。丰田从一开始便清楚,TMMK成功的关键在于公司能否在短期之内在TMMK建立起丰田模式。
当时,他们还未将这种风格称为“丰田模式”,只是简单称之为“丰田的行事方式”。但丰田生产方式在那时已经被明确提出,并成了公司的理念,尤其在质量和人力资源管理领域。这一理念的作用不止这些,它贯穿于公司的每一项活动之中。正如大卫作为生产团队领导人接受的培训一样,乔治城新厂的每一位领导者都要被派往丰田市接受培训,他们不仅要在TMMK的生产中心堤工厂(Tsutsumi)学习,还要到公司总部接受会计、采购、社区关系、设施管理等对应领域的培训。比如,TMMK社区关系职业人员学会了丰田公司与丰田市共事和合作的方式。为什么这也要学习?是不是丰田公司认为它与丰田市的关系模式是最佳的实践标杆?是不是丰田认为它与日本名古屋外围的当地社区的关系模式是值得位于肯塔基中部地区的TMMK效仿的榜样?当然,这些都不是原因。真正的原因是,丰田深知它的文化——它的企业文化而不是它的“日本色彩”才是其主要特点,而正是它的企业文化界定了公司在每个层面、每个部门的运作风格。大卫和他的同事们当时并未听说过“丰田模式”这种说法,但是公司当时传授给他们的正是“丰田风格”——深入所有层面,包括技术层面和社会层面。
而这也正是杰弗瑞和大卫能够组成一个伟大的团队来编写这本实践指南的原因所在。杰弗瑞对社会技术体系尤其是丰田公司多年的学术研究经验,大卫在工厂现场践行丰田模式的一线经验,两者结合起来共同为读者提供既切合实际而又不乏深入理论的实践指南。
在经验丰富的丰田生产方式的老师看来,任何试图将“丰田模式”付诸笔端的尝试都是一种富有争议的行径,因为像丰田模式这种充满大量隐性知识的系统,实在难以用语言来抓住其精髓。然而,这并不是因为丰田模式有多么神秘,以至于只能意会而无法言传,其实原因很简单:这种方式只能通过“边学边实践”来学习。同样,即使你成功地用语言准确地将其表达出来,但仍然存在误导某些读者的风险。企业管理人员都是聪明人且通常都受过高等教育,他们习惯通过书籍、研讨会、管理人员培训等方式了解最新的管理趋势。试图通过这些方式来学习丰田生产方式的潜在危险在于,有些读者可能会在读了某些东西之后,就以为自己什么都会了。
看似简单的丰田模式其实颇具迷惑性,人们往往在读完一条简单的原则之后,便自以为是地说:“我当然知道……”而在这本书中,杰弗瑞和大卫采用的方法就是试图帮助你避免产生这种倾向。这本书建议读者不要看完书后就万事大吉,自以为“我都掌握了”。你应该亲自践行你所阅读的内容:阅读、尝试、反思和学习。
约翰·舒克美国精益企业研究所总裁
文摘
版权页:
在试图向各企业传授均衡化的生产模式和方法时,我们最常见到的反应是:“销售部门有自己的动机,它在公司始终处于第一位。它销售一切能推销出去的东西,而我们制造部门必须按照它的期望进行生产。但是,销售情况每周的变化很大,变化幅度有时甚至达到了100%。”然而,经过仔细研究数据,我们通常发现,实际需求要比制造部门所看到的平稳得多。
在一家制造多种不同类型文件柜的办公用具制造公司,客户的订单非常不稳定。而公司的政策是100%按订单生产,因此在接到订单之后,制造部门总是像救火一样急于赶工。这导致在生产的各个阶段都产生了大量的存货,并且流程缺乏明确的生产节拍。当被问及给订购文件柜的客户多久的提前期时,他们给出的答案是6~8周。于是,这家工厂总是在订单接踵而至之后疯狂地赶工,而却在6~8周的提前期里未进行任何创造价值的活动。为什么不用这一缓冲时间来平衡生产计划表呢?如果存在成品的文件柜存货,至少是高产量的文件柜存货,则完全可以将6~8周的提前期缩短,使生产计划表均衡化,以创造更为高效的流程。实际上,这家工厂围绕三大产品系列价值流对生产进行了重组,并使用一些成品产品存货来均衡生产计划表,结果不仅释放了工厂1/4的产能以开发新业务,还极大地降低了总体存货水平、提前期和总成本。
要实现一项看似合理的计划,并不像听起来那么简单。家具制造商不仅需要改变销售人员下单的方式,还要改变配送流程和生产控制部门安排生产的方式。这些任务由不同的职能部门负责,这些部门实行既定的方式已经有多年历史。他们不相信新的生产方式能够行得通,预言这一方式最终将以失败告终。克服这些阻力需要对未来状态充满强烈的愿景并得到高层的大力支持。
《丰田模式(实践手册篇):实施丰田4P的实践指南(珍藏版)》由机械工业出版社出版。《丰田模式(实践手册篇):实施丰田4P的实践指南(珍藏版)》为你提供了多种分析工具、工作表和练习——其中许多改编自丰田的真实文件——以便你可以为你的公司制定最有效的方法。更为重要的是,你可以理解精益工具和方法背后所蕴含的思维方式,从而将丰田的4P模型全面而永久地融入你的组织之中。
作者简介
作者简介杰弗瑞·莱克现任密歇根大学工业与运营工程系教授,并担任该校日本技术管理项目主任。代表作包括《丰田模式:精益制造的14项管理原则》(由麦格劳-希尔公司于2004年出版,该书曾荣获2005年“新乡奖”、美国工业工程协会2005年度图书等殊荣)。他所编著的《迈向精益》(Becoming Lean)因对制造业提出精辟研究而赢得1998年“新乡奖”。此外,他也凭借的研究贡献分别在1995年、1996年和1997年赢得“新乡奖”。莱克的其他著作包括Engineered in Japan、Concurrent Engineering Effectiveness、Remade in America,以及与詹姆斯·摩根(James Morgan)合著的《高性能产品开发》(High Performance Product Development)。莱克经常应邀为企业主管举办讲座,并以个人名义或与他人共同创办的管理顾问公司Optiprise Inc.首席顾问的身份担任精益顾问,近期客户包括戴姆勒-克莱斯勒、麦塔尔萨、丹佛斯、力拓矿业、卡特彼勒亚太区分公司、本特勒汽车、法马通公司、诺斯罗普·格鲁门公司舰船系统部、杰克逊维尔海空维修基地、美国空军、朴次茅斯海军船厂等。
大卫·梅尔曾作为丰田肯塔基州乔治城工厂塑料铸模部聘任的第一批团队领导人之一进行丰田生产方式的学习。他先后在日本和肯塔基州接受丰田生产方式专家长达十年的培训和指导,其中包括多名协调员负责的全职培训。离开丰田之后,他创建了美国精益顾问公司(Lean Associates),致力于为追求实行丰田生产方式的企业提供支持服务。
大卫为《精益制造:车间现场指南》(Lean Manufacturing: A Plant Floor Guide)一书撰写了两章内容,并担任培训师长达8年。梅尔曾举办标准化作业、绘制价值流图、制造工程师协会精益基础入门、“新乡奖”研讨会等培训讲习班。他曾为各行各业的公司提供咨询与指导,涉及领域包括汽车、航空航天、木材和塑料产品加工、化学产品加工、金属加工、制造生产、焊接及制造业和非制造业的装配作业等。梅尔擅长在组织内部实行丰田生产方式,使组织实现精益转型。
目录
推荐序
作者简介
前言
致谢
第一篇向丰田学习
第1章实践指南的背景 2
为何撰写本书 2
本书的篇章结构 5
丰田模式原则综述 7
如何使用本书 13
第二篇你的公司为何存在
第2章明确公司目的并开始践行 16
你公司的理念是什么 16
内部和外部的目的感 17
创建你的理念 22
践行你的理念 24
与员工和合作伙伴签订社会契约 25
保持目的的连续性 26
第三篇在整个企业中创建精益流程
第3章开启减少浪费之旅 30
精益就是杜绝浪费 30
建立减少浪费的长期理念 34
价值流图法 35
价值流图法的益处 38
绘制现状价值流图 39
绘制现状价值流图时必须了解你的目标 39
价值流图法的局限性 44
按部就班地创建无间断流程 44
相继的与同步的持续改进 48
第4章创建初步的流程稳定性 52
首先实现基本的稳定性 52
不稳定的指标 53
拨云见日 54
稳定性的目标 55
实现稳定性的策略 56
识别并消除大浪费 56
站在圆圈内的练习 57
以标准化作业作为识别和消除浪费的工具 57
5S和工作场所组织 60
整合浪费活动,以获取收益 61
改进运行效率 66
通过隔离法减少变异 68
均衡工作量,为创建无间断流程和标准化奠定基础 72
第5章创建无间断流程 74
单件流是理想 74
为何要创建无间断流程 76
少即多:控制生产过剩,减少浪费 77
创建无间断流程的策略 83
单件流 83
实现无间断流程的主要标准 84
拉动式制度 87
复杂的单件流 91
定制制造业的拉动式制度 92
在独立的作业步骤之间创建拉动 95
无间断流程、拉动式制度和杜绝浪费 100
第6章建立标准化流程与程序 104
标准化是强制性的吗 104
标准化作业抑或是作业标准 106
标准化的目标 107
建立标准化流程和程序的策略 109
标准化的类型 110
质量、安全与环境标准 112
标准规范 113
标准程序 114
对标准化作业的误解 114
标准化作业 117
标准化作业文件 118
制定标准化作业面临的挑战 123
标准化作业的审核 125
以标准化作业作为持续改善的基线 127
以生产节拍作为设计参数 128
可视化控制的重要性 130
标准化作业是一种消除浪费的工具 133
第7章均衡化:向乌龟学习,不要像兔子 136
均衡化的矛盾 136
均衡化为资源规划提供了标准化的核心 137
为什么迫使自己实行均衡化 138
平稳上游流程的需求 139
如何制定基本均衡化的生产计划表 142
渐进式均衡化和高级均衡化 147
渐进式均衡化 148
控制点 148
存货管理的控制点 149
均衡化的生产计划表决定补货作业 150
产品种类繁多时的“切片切块”多维分析法 151
均衡化需要全企业的共同努力 156
第8章建立一种暂停作业以解决问题的文化 160
形成文化 161
自动化的作用:自我监控的机器 165
解决问题的循环 167
将生产线暂停时间降至最低 171
将质量检查内建于每一项工作之中 173
差错预防技术 174
创建支持架构 183
第9章使技术与员工和精益流程相匹配 186
倒退到算盘时代 186
你如何看待技术、员工与流程 188
调整技术以适应你的员工和经营理念 191
对比不同的技术采纳模型 193
正确地运用技术 200
第四篇培养杰出的员工和合作伙伴
第10章培养彻底了解公司体系的领导者 206
成功始于领导能力 206
丰田公司领导能力的重要意义 207
丰田公司乔治城工厂生产线的领导结构 209
丰田公司乔治城工厂参谋领导结构 211
领导者的必备条件 211
一个典型工作日中团队领导人的职责 213
创建生产领导结构 219
领导干部的选拔 220
培养领导者 224
领导者的接替计划 225
第11章培养杰出的团队成员 228
我们不只制造汽车,也在塑造人 228
从选拔正确的员工开始 229
让团队成员融入你的公司文化 232
工作指导培训:培养杰出技能水平的关键 234
制定培训计划,追踪工作表现 241
立足长远利益培养团队成员 244
质量圈 245
丰田的建议体系 247
培养团队成员承担领导角色 249
联谊活动增强团队凝聚力 251
投资发展公司各个领域的技能 251
第12章将供应商和合作伙伴发展为企业的外延 256
在全球竞争环境中的供应商伙伴 256
短期的节约成本与长期的伙伴关系 257
丰田模式下的供应商伙伴 259
供应商伙伴关系的七个特点 261
建立精益的扩展企业 277
供应商管理的传统模式与精益模式对比 281
第五篇从根本上解决问题,实现持续学习
第13章丰田模式解决问题的方法 292
不只是解决问题 292
每个问题都是改善的机会 294
讲述解决问题的故事 297
第14章彻底了解情况并定义问题 307
认真瞄准后再开枪 307
找出真正的问题,获得最显著的成效 311
反方向考察问题 317
定义问题 317
建立强大的支持依据 320
第15章进行彻底的根本原因分析 324
有效分析的原则 324
探索可解决的问题原因 329
将根本原因分析提炼成最简单形式 331
一幅图胜过千言万语 332
全部集中汇总:一页A3纸报告 333
深入发掘可能的原因 335
第16章考虑各种可行的解决方案,建立共识 337
广泛考虑各种可能性 337
评估的简单性、成本、控制范围和快速实施能力 339
建立共识 340
测试想法的有效性 341
选择最佳的解决方案 342
正确定义问题,解决方法则水到渠成 342
第17章计划—实施—检查—处理 344
计划:制定行动计划 345
实施:实施解决方案 348
检查:检验成果 348
处理:对解决方案和行动计划做出必要调整 350
处理:确定未来步骤 351
最终实施行动 352
第18章使用A3纸报告来说明情况 355
撰写报告时,简单的形式可能带来更好的效果 355
确定如何使用A3纸报告 356
解决问题A3纸报告流程 358
A3纸报告概述 360
版式设计建议 361
解决问题情况的A3纸报告最终版 363
A3纸报告的最后评论 366
第六篇管理变革
第19章实施精益解决方案的策略与方法 370
从哪里入手 370
精益的执行层级、策略和工具 371
耐心去做 394
第20章领导变革 403
我们能避免精益变革中涉及的政治因素吗 403
高层、中层与基层的领导 406
能否靠评估指标来实现精益 424
改变行为以改变文化 430
把你的学习推广至事业伙伴 434
现在请尝试并全力以赴 437
译后记 442
序言
推荐序当杰弗瑞·莱克和大卫·梅尔让我为这本实践指南作序时,我立刻热情地答应了下来,但旋即又有些许担心。一本关于丰田模式的“实践指南”?到底什么是实践指南,又该如何来形容丰田模式?像一本提供各种食谱的烹饪书籍,还是一本路线图?但是通过阅读本书,读者会发现这根本不是什么烹饪书籍或路线图,而是一个能够指明方向的指南针,它能够帮助你找到属于自己的道路。而作者杰弗瑞和大卫则是你的领路人,他们装备齐全,定能为你提供莫大的帮助,我对此深信不疑。碰巧的是,当杰弗瑞和大卫首次参加在丰田市举办的全球高级工商管理项目时,我都在场,只不过与他们每个人见面的场景不同而已。和杰弗瑞见面的时候,我当时还在丰田工作,而他则是密歇根大学的一名教授,正在进行社会技术体系方面的研究,其实,早在他还是马萨诸塞大学的一名学生时,他就已经开始了这项研究。与大卫·梅尔的碰面则是在我向丰田在美国的新员工介绍丰田生产方式的时候。当时,他正在车间现场学习丰田模式——或许,你也应该像他一样,到车间现场去学习。
杰弗瑞与丰田的结缘源自正规教育和后续的研究,他对工业的“软科学”与“硬科学”拥有同样的兴趣和经验。作为一名工业工程师和东北大学(美国)带薪实习的学生,杰弗瑞在通用食品公司(General Foods Corporation)工作,负责运营研究、工厂布局等工业工程工作,然而最令他感兴趣的却是一家位于托皮卡的狗粮工厂。这家工厂依据社会技术体系——社会与技术系统联合设计而成,围绕实行自我管理的不同团队组织创建。在马萨诸塞大学获得博士学位之后,杰弗瑞加入了这所大学的工业与运营工程学院,并一直在那里任教至今。通过和大卫·科尔(David Cole)、罗伯特·科尔(Robert Cole)等人一起参加著名的密歇根大学美日汽车研究项目,杰弗瑞对汽车行业和日本的研究进一步深入发展,并进而接触到丰田及丰田生产方式。在丰田,他发现自己研究多年的社会科技体系得到了实际应用。也正是在这里,他认为他终于找到了一个将社会和科技体系实现真正融合的组织。
杰弗瑞与政治学教授约翰·坎贝尔(John Campbell)及密歇根商学院的布莱恩·塔尔伯特(Brian Talbot)教授共同创建了日本技术管理项目(我曾经有幸为其工作多年),旨在研究日本的成功组织如何进行技术管理。他们在研究过程中认识到,众多日本企业在各自领域内的竞争优势并非源自“硬”技术(比如,丰田所使用的锻压机和机器人与福特所使用的锻压机和机器人源自同一家供应商),关键在于对相同技术的管理方式。因此,这个项目重点关注的是一些企业(尤其是丰田)将技术与人、机构、产品和策略实现整体融合的方式。经研究发现,这些企业的与众不同之处在于它们的社会科技体系,尽管很少有企业会用这样的术语来解释这个问题。
大卫的实地学习机会从工厂现场开始。1987年夏天,他成为丰田肯塔基工厂(TMMK)第一批派往丰田市的一线监管员团队中的一员,前往丰田接受管理培训。那时,丰田已经“实践”过了以合资形式创建的新联合汽车制造有限公司(NUMMI),而乔治城是丰田在日本境外第一家实现完全自主经营的工厂。与肯塔基州政府合作,丰田开发了一套全面的评估方案来选拔应聘首批3 000个工作岗位的10万名应征者!而大卫是在首轮选拔中便脱颖而出的基层领导人员之一。此次选拔过程异常严格,但这只是整个培训开发流程的序曲,在接下来的几年里,大卫又接受了更多紧张而充实的培训。丰田从一开始便清楚,TMMK成功的关键在于公司能否在短期之内在TMMK建立起丰田模式。
当时,他们还未将这种风格称为“丰田模式”,只是简单称之为“丰田的行事方式”。但丰田生产方式在那时已经被明确提出,并成了公司的理念,尤其在质量和人力资源管理领域。这一理念的作用不止这些,它贯穿于公司的每一项活动之中。正如大卫作为生产团队领导人接受的培训一样,乔治城新厂的每一位领导者都要被派往丰田市接受培训,他们不仅要在TMMK的生产中心堤工厂(Tsutsumi)学习,还要到公司总部接受会计、采购、社区关系、设施管理等对应领域的培训。比如,TMMK社区关系职业人员学会了丰田公司与丰田市共事和合作的方式。为什么这也要学习?是不是丰田公司认为它与丰田市的关系模式是最佳的实践标杆?是不是丰田认为它与日本名古屋外围的当地社区的关系模式是值得位于肯塔基中部地区的TMMK效仿的榜样?当然,这些都不是原因。真正的原因是,丰田深知它的文化——它的企业文化而不是它的“日本色彩”才是其主要特点,而正是它的企业文化界定了公司在每个层面、每个部门的运作风格。大卫和他的同事们当时并未听说过“丰田模式”这种说法,但是公司当时传授给他们的正是“丰田风格”——深入所有层面,包括技术层面和社会层面。
而这也正是杰弗瑞和大卫能够组成一个伟大的团队来编写这本实践指南的原因所在。杰弗瑞对社会技术体系尤其是丰田公司多年的学术研究经验,大卫在工厂现场践行丰田模式的一线经验,两者结合起来共同为读者提供既切合实际而又不乏深入理论的实践指南。
在经验丰富的丰田生产方式的老师看来,任何试图将“丰田模式”付诸笔端的尝试都是一种富有争议的行径,因为像丰田模式这种充满大量隐性知识的系统,实在难以用语言来抓住其精髓。然而,这并不是因为丰田模式有多么神秘,以至于只能意会而无法言传,其实原因很简单:这种方式只能通过“边学边实践”来学习。同样,即使你成功地用语言准确地将其表达出来,但仍然存在误导某些读者的风险。企业管理人员都是聪明人且通常都受过高等教育,他们习惯通过书籍、研讨会、管理人员培训等方式了解最新的管理趋势。试图通过这些方式来学习丰田生产方式的潜在危险在于,有些读者可能会在读了某些东西之后,就以为自己什么都会了。
看似简单的丰田模式其实颇具迷惑性,人们往往在读完一条简单的原则之后,便自以为是地说:“我当然知道……”而在这本书中,杰弗瑞和大卫采用的方法就是试图帮助你避免产生这种倾向。这本书建议读者不要看完书后就万事大吉,自以为“我都掌握了”。你应该亲自践行你所阅读的内容:阅读、尝试、反思和学习。
约翰·舒克美国精益企业研究所总裁
文摘
版权页:
在试图向各企业传授均衡化的生产模式和方法时,我们最常见到的反应是:“销售部门有自己的动机,它在公司始终处于第一位。它销售一切能推销出去的东西,而我们制造部门必须按照它的期望进行生产。但是,销售情况每周的变化很大,变化幅度有时甚至达到了100%。”然而,经过仔细研究数据,我们通常发现,实际需求要比制造部门所看到的平稳得多。
在一家制造多种不同类型文件柜的办公用具制造公司,客户的订单非常不稳定。而公司的政策是100%按订单生产,因此在接到订单之后,制造部门总是像救火一样急于赶工。这导致在生产的各个阶段都产生了大量的存货,并且流程缺乏明确的生产节拍。当被问及给订购文件柜的客户多久的提前期时,他们给出的答案是6~8周。于是,这家工厂总是在订单接踵而至之后疯狂地赶工,而却在6~8周的提前期里未进行任何创造价值的活动。为什么不用这一缓冲时间来平衡生产计划表呢?如果存在成品的文件柜存货,至少是高产量的文件柜存货,则完全可以将6~8周的提前期缩短,使生产计划表均衡化,以创造更为高效的流程。实际上,这家工厂围绕三大产品系列价值流对生产进行了重组,并使用一些成品产品存货来均衡生产计划表,结果不仅释放了工厂1/4的产能以开发新业务,还极大地降低了总体存货水平、提前期和总成本。
要实现一项看似合理的计划,并不像听起来那么简单。家具制造商不仅需要改变销售人员下单的方式,还要改变配送流程和生产控制部门安排生产的方式。这些任务由不同的职能部门负责,这些部门实行既定的方式已经有多年历史。他们不相信新的生产方式能够行得通,预言这一方式最终将以失败告终。克服这些阻力需要对未来状态充满强烈的愿景并得到高层的大力支持。
ISBN | 9787111531005 |
---|---|
出版社 | 机械工业出版社 |
作者 | 杰弗瑞·莱克 (Jeffrey Liker) |
尺寸 | 16 |