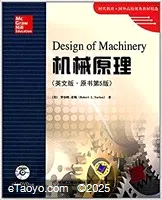
编辑推荐
《时代教育·国外高校优秀教材精选:机械原理(英文版·原书第5版)》由机械工业出版社出版。
名人推荐
Robert L.Noton所著的《Design of machinery》是在美国广泛应用的《机械原理》教材(虽然英文原书名为“Design of machinery”,但是从内容看,按国内的习惯应该是机械原理)。它已被翻译成多国语言。第5版继承了前几版的形式,将主要内容分为机构运动学篇和机构动力学篇。虽然本书的基本内容在国内教材中多有涉及,但是本书综合设计的特色却是这些教材所欠缺的。书中不仅深入浅出地介绍了机械原理的基本理论,而且巧妙地利用若干个典型实例将这些理论的应用循序渐进地贯穿于全书。本书对于课后习题也进行了同样的处理。后置章节的习题往往是前置章节习题的进一步拓展,而且部分还涉及了后续课程的内容。这样的处理充分表明了不同章节、甚至不同课程所授理论之间的有机联系,较好体现,本书综合设计的理念。围绕书中内容开发的电子资源是本书的另一特色,附带的光盘提供了大量动画、视频、虚拟横型、程序和虚拟实验室,不仅为教师和学生提供了丰富的教学和学习资源,而且大大丰富和创新了机械类课程教材的内容和形式。
——华南理工大学 黄平
作者简介
作者:(美国)罗伯特·诺顿(Robert L.Norton)
目录
Preface to the Fifth Edition
Preface to the First Edition
PART Ⅰ KINEMATICS OF MECHANISMS
Chapter 1 Introduction
1.0 Purpose
1.1 Kinematics and Kinetics
1.2 Mechanisms and Machines
1.3 A Brlef History of Kinematics
1.4 Applications of Kinematics
1.5 The Design Process
Design, Invention, Creotivity
Identification of Need
Background Research
Goal Statement
Performance Specifications
Ideation and Invention
Analysis
Selection
Detoiled Design
Prototyplng ond Testing
Production
1.6 Other Approaches to Design
Axlomatic Design
1.7 Multiple Solutions
1.8 Human Factors Engineering
1.9 The Engineering Report
1.10 Units
1.11 A Design Case Study
Educcrting for Creativity In Engineering
1.12 What's to Come
1.13 Resources with This Text
Programs
Videos
1.14 References
1.15 Bibliography
Chapter 2 Kinematics Fundamentals
2.0 Introduction
2.1 Degrees of Freedom (DOF) or Mobillty
2.2 Types of Motion
2.3 Links, Joints, and Kinematic Chains
2.4 Drawing Kinematic Diagrams
2.5 Determining Degree of Freedom or Moblllty
Degree of Freedom (Mobility) In Planar Meohonisms
Degree of Freedom (Mobility) in Spatial Mechanisms
2.6 Mechanisms and Structures
2.7 Number Synthesis
2.8 Paradoxes
2.9 Isomers
2.10 Linkage Transformation
2.11 Intermittent Motion
2.12 Inversion
2.13 The Grashof Condition
Classification of the Fourbar Linkage
2.14 Linkages of More Than Four Bars
Geared Fivebar Linkages
Slxbar Linkages
Grashof—Type Ratatabtltiy Criteria for Higher—Order Linkages
2.15 Springs as Links
2.16 Compliant Mechanisms
2.17 Micro Electro—Mechanical Systems (MEMS)
2.18 Practical Considerations
Pin Joints versus Sliders and Half Joints
Cantilever or Straddle Mount?
Short Links
Beating Ratio
Commercial Slides
Linkages versus Cams
2.19 Motors and Drivers
Electric Motors
Air and Hydraulic Motors
Air and Hydraulic Cylinders
Solenoids
2.20 References
2.21 Problems
Chapter 3 Graphical Linkage Synthesis
3.0 Introduction
3.1 Synthesis
3.2 Function, Path, and Motion Generation
3.3 Limiting Conditions
3.4 Dimensional Synthesis
Two—Position Synthesis
Three—Position Synthesis with Specified Moving Pivots
Three—Pasifion Synthesis with Alternate Moving Pivots
Three—Position Synthesis with Specified Fixed Pivots
Position Synthesis for More Than Three Positions
3.5 Quick—Return Mechanisms
Fourbar Quick—Return
Slxbar Quick—Return
3.6 Coupler Curves
3.7 Cognates
Parallel Motion
Geared Flvebar Cognates of the Fourbar
3.8 Straight—Line Mechanisms
Designing Optimum Straight—Line Fourbar Linkages
3.9 Dwell Mechanisms
Single—Dwell Linkages
Double—Dwell Linkages
3.10 Other Useful Unkages
Constant Velocity Piston Motion
Large Angular Excursion Rocker Motion
Remote Center Circular Motion
3.11 References
3.12 Bibliography
3.13 Problems
3.14 Projects
Chapter 4 Position Analysis
4.0 Introduction
4.1 Coordinate Systems
4.2 Position and Displacement
Position
Coordinate Transformation
Displacement
4.3 Translation, Rotation, and Complex Motion
Translation
Rotation
Complex Motion
Theorems
4.4 Graphical Position Analysis of Linkages
4.5 Algebraic Position Analysis of Unkages
Vector Loop Representation of Unkages
Complex Numbers as Veotots
The Vector Loop Equation for a Fourbar Linkage
4.6 The Fourbar Crank—Slider Position Solution
4.7 The Fourbar Slider—Crank Position Solution
4.8 An Inverted Crank—Slider Position Solution
4.9 Unkages of More Than Four Bars
The Geared Fivebar Linkage
Sixbar Linkages
4.10 Position of Any Point on a Linkage
4.11 Transmission Angles
Extreme Values of the Transmission Angle
4.12 Toggle Positions
4.13 Circuits and Branches In Linkages
4.14 Newton—Raphson Solution Method
One—Dimensional Root—Finding (Newton's Method)
Multidimensional Root—Finding (Newton—Raphson Method)
Newton—Raphson Solution for the Fourbar Linkage
Equation Solvers
4.15 References
4.16 Problems
Chapter 5 Analytical Linkage Synthesis
5.0 Introduction
5.1 Types of Kinematic Synthesis
5.2 Two—Position Synthesis for Rocker Output
5.3 Precision Points
5.4 Two—Position Motion Generation by Analytical Synthesis
5.5 Comparison of Analytical and Graphical Two—Position Synthesis
5.6 Simultaneous Equation Solution
5.7 Three—Position Motion Generation by Analytical Synthesis
5.8 Comparison of Analytical and Graphical Three—Position Synthesis
5.9 Synthesis for a Specified Fixed Pivot Location
5.10 Center—Point and Circle—Point Circles
5.11 Four— and Five—Posltion Analytical Synthesis
5.12 Analytical Synthesis of a Path Generator with Prescribed Timing
5.13 Analytical Synthesis of a Fourbar Function Generator
5.14 Other Unkage Synthesis Methods
Precision Point Methods
Coupler Curve Equation Methods
Optimization Methods
5.15 References
5.16 Problems
Chapter 6 Velocity Analysis
6.0 introduction
6.1 Definition of Velocity
6.2 Graphical Velocity Analysis
6.3 Instant Centers of Velocity
6.4 Velocity Analysis with instant Centers
Angular Velocity Ratio
Mechanical Advantage
Using instant Centers In Linkage Design
6.5 Centrodes
A "Linkless" Linkage
Cusps
6.6 Velocity of Slip
6.7 Analytical Solutions for Velocity Analysis
The Fourbar Pin—Jointed Linkage
The Fourbar Crank—Slider
The Fourbar Slider—Crank
The Fourbar Inverted Crank—Slider
6.8 Velocity Analysis of the Geared Flvebar Linkage
6.9 Velocity of Any Point on a Unkage
6.10 References
6.11 Problems
Chapter 7 Acceleration Analysis
7.0 Introduction
7.1 Definition of Acceleration
7,2 Graphical Acceleration Analysis
7.3 Analytical Solutions for Acceleration Analysis
The Fourbar Pin—Jointed Linkage
The Fourbar Crank—Slider
The Fourbar Slider—Crank
Coriolis Acceleration
The Fourbar Inverted Crank—Slider
7.4 Acceleration Analysis of the Geared Fivebar Unkage
7.5 Acceleration of Any Point on a Linkage
7.6 Human Tolerance of Acceleration
7.7 Jerk
7.8 Linkages of N Bars
7.9 Reference
7.10 Problems
7.11 Virtual Laboratory
……
Chapter 8 Cam Design
Chapter 9 Gear Trains
PART Ⅱ DYNAMICS OF MACHINERY
Appendices
文摘
版权页:
插图:
Figure 3—17b* (p.126) shows a "fleshed out" linkage drawn on top of the H&N atlas page to illustrate its relationship to the atlas information.The double circles in Figure 3—17a (p.126) define the fixed pivots.The crank is always of unit length.The ratios of the other link lengths to the crank are given on each page.The actual link lengths can be scaled up or down to suit your package constraints and this will affect the size but not the shape of the coupler curve.Any one of the ten coupler points shown can be used by incorporating it into a triangular coupler link.The location of the chosen coupler point can be scaled from the atlas and is defined within the coupler by the position vector R whose constant angle φ is measured with respect to the line of centers of the coupler.The H&N coupler curves are shown as dashed lines.Each dash station represents five degrees of crank rotation.So, for an assumed constant crank velocity, the dash spacing is proportional to path velocity.The changes in velocity and the quick—return nature of the coupler path motion can be clearly seen from the clash spacing.
《时代教育·国外高校优秀教材精选:机械原理(英文版·原书第5版)》由机械工业出版社出版。
名人推荐
Robert L.Noton所著的《Design of machinery》是在美国广泛应用的《机械原理》教材(虽然英文原书名为“Design of machinery”,但是从内容看,按国内的习惯应该是机械原理)。它已被翻译成多国语言。第5版继承了前几版的形式,将主要内容分为机构运动学篇和机构动力学篇。虽然本书的基本内容在国内教材中多有涉及,但是本书综合设计的特色却是这些教材所欠缺的。书中不仅深入浅出地介绍了机械原理的基本理论,而且巧妙地利用若干个典型实例将这些理论的应用循序渐进地贯穿于全书。本书对于课后习题也进行了同样的处理。后置章节的习题往往是前置章节习题的进一步拓展,而且部分还涉及了后续课程的内容。这样的处理充分表明了不同章节、甚至不同课程所授理论之间的有机联系,较好体现,本书综合设计的理念。围绕书中内容开发的电子资源是本书的另一特色,附带的光盘提供了大量动画、视频、虚拟横型、程序和虚拟实验室,不仅为教师和学生提供了丰富的教学和学习资源,而且大大丰富和创新了机械类课程教材的内容和形式。
——华南理工大学 黄平
作者简介
作者:(美国)罗伯特·诺顿(Robert L.Norton)
目录
Preface to the Fifth Edition
Preface to the First Edition
PART Ⅰ KINEMATICS OF MECHANISMS
Chapter 1 Introduction
1.0 Purpose
1.1 Kinematics and Kinetics
1.2 Mechanisms and Machines
1.3 A Brlef History of Kinematics
1.4 Applications of Kinematics
1.5 The Design Process
Design, Invention, Creotivity
Identification of Need
Background Research
Goal Statement
Performance Specifications
Ideation and Invention
Analysis
Selection
Detoiled Design
Prototyplng ond Testing
Production
1.6 Other Approaches to Design
Axlomatic Design
1.7 Multiple Solutions
1.8 Human Factors Engineering
1.9 The Engineering Report
1.10 Units
1.11 A Design Case Study
Educcrting for Creativity In Engineering
1.12 What's to Come
1.13 Resources with This Text
Programs
Videos
1.14 References
1.15 Bibliography
Chapter 2 Kinematics Fundamentals
2.0 Introduction
2.1 Degrees of Freedom (DOF) or Mobillty
2.2 Types of Motion
2.3 Links, Joints, and Kinematic Chains
2.4 Drawing Kinematic Diagrams
2.5 Determining Degree of Freedom or Moblllty
Degree of Freedom (Mobility) In Planar Meohonisms
Degree of Freedom (Mobility) in Spatial Mechanisms
2.6 Mechanisms and Structures
2.7 Number Synthesis
2.8 Paradoxes
2.9 Isomers
2.10 Linkage Transformation
2.11 Intermittent Motion
2.12 Inversion
2.13 The Grashof Condition
Classification of the Fourbar Linkage
2.14 Linkages of More Than Four Bars
Geared Fivebar Linkages
Slxbar Linkages
Grashof—Type Ratatabtltiy Criteria for Higher—Order Linkages
2.15 Springs as Links
2.16 Compliant Mechanisms
2.17 Micro Electro—Mechanical Systems (MEMS)
2.18 Practical Considerations
Pin Joints versus Sliders and Half Joints
Cantilever or Straddle Mount?
Short Links
Beating Ratio
Commercial Slides
Linkages versus Cams
2.19 Motors and Drivers
Electric Motors
Air and Hydraulic Motors
Air and Hydraulic Cylinders
Solenoids
2.20 References
2.21 Problems
Chapter 3 Graphical Linkage Synthesis
3.0 Introduction
3.1 Synthesis
3.2 Function, Path, and Motion Generation
3.3 Limiting Conditions
3.4 Dimensional Synthesis
Two—Position Synthesis
Three—Position Synthesis with Specified Moving Pivots
Three—Pasifion Synthesis with Alternate Moving Pivots
Three—Position Synthesis with Specified Fixed Pivots
Position Synthesis for More Than Three Positions
3.5 Quick—Return Mechanisms
Fourbar Quick—Return
Slxbar Quick—Return
3.6 Coupler Curves
3.7 Cognates
Parallel Motion
Geared Flvebar Cognates of the Fourbar
3.8 Straight—Line Mechanisms
Designing Optimum Straight—Line Fourbar Linkages
3.9 Dwell Mechanisms
Single—Dwell Linkages
Double—Dwell Linkages
3.10 Other Useful Unkages
Constant Velocity Piston Motion
Large Angular Excursion Rocker Motion
Remote Center Circular Motion
3.11 References
3.12 Bibliography
3.13 Problems
3.14 Projects
Chapter 4 Position Analysis
4.0 Introduction
4.1 Coordinate Systems
4.2 Position and Displacement
Position
Coordinate Transformation
Displacement
4.3 Translation, Rotation, and Complex Motion
Translation
Rotation
Complex Motion
Theorems
4.4 Graphical Position Analysis of Linkages
4.5 Algebraic Position Analysis of Unkages
Vector Loop Representation of Unkages
Complex Numbers as Veotots
The Vector Loop Equation for a Fourbar Linkage
4.6 The Fourbar Crank—Slider Position Solution
4.7 The Fourbar Slider—Crank Position Solution
4.8 An Inverted Crank—Slider Position Solution
4.9 Unkages of More Than Four Bars
The Geared Fivebar Linkage
Sixbar Linkages
4.10 Position of Any Point on a Linkage
4.11 Transmission Angles
Extreme Values of the Transmission Angle
4.12 Toggle Positions
4.13 Circuits and Branches In Linkages
4.14 Newton—Raphson Solution Method
One—Dimensional Root—Finding (Newton's Method)
Multidimensional Root—Finding (Newton—Raphson Method)
Newton—Raphson Solution for the Fourbar Linkage
Equation Solvers
4.15 References
4.16 Problems
Chapter 5 Analytical Linkage Synthesis
5.0 Introduction
5.1 Types of Kinematic Synthesis
5.2 Two—Position Synthesis for Rocker Output
5.3 Precision Points
5.4 Two—Position Motion Generation by Analytical Synthesis
5.5 Comparison of Analytical and Graphical Two—Position Synthesis
5.6 Simultaneous Equation Solution
5.7 Three—Position Motion Generation by Analytical Synthesis
5.8 Comparison of Analytical and Graphical Three—Position Synthesis
5.9 Synthesis for a Specified Fixed Pivot Location
5.10 Center—Point and Circle—Point Circles
5.11 Four— and Five—Posltion Analytical Synthesis
5.12 Analytical Synthesis of a Path Generator with Prescribed Timing
5.13 Analytical Synthesis of a Fourbar Function Generator
5.14 Other Unkage Synthesis Methods
Precision Point Methods
Coupler Curve Equation Methods
Optimization Methods
5.15 References
5.16 Problems
Chapter 6 Velocity Analysis
6.0 introduction
6.1 Definition of Velocity
6.2 Graphical Velocity Analysis
6.3 Instant Centers of Velocity
6.4 Velocity Analysis with instant Centers
Angular Velocity Ratio
Mechanical Advantage
Using instant Centers In Linkage Design
6.5 Centrodes
A "Linkless" Linkage
Cusps
6.6 Velocity of Slip
6.7 Analytical Solutions for Velocity Analysis
The Fourbar Pin—Jointed Linkage
The Fourbar Crank—Slider
The Fourbar Slider—Crank
The Fourbar Inverted Crank—Slider
6.8 Velocity Analysis of the Geared Flvebar Linkage
6.9 Velocity of Any Point on a Unkage
6.10 References
6.11 Problems
Chapter 7 Acceleration Analysis
7.0 Introduction
7.1 Definition of Acceleration
7,2 Graphical Acceleration Analysis
7.3 Analytical Solutions for Acceleration Analysis
The Fourbar Pin—Jointed Linkage
The Fourbar Crank—Slider
The Fourbar Slider—Crank
Coriolis Acceleration
The Fourbar Inverted Crank—Slider
7.4 Acceleration Analysis of the Geared Fivebar Unkage
7.5 Acceleration of Any Point on a Linkage
7.6 Human Tolerance of Acceleration
7.7 Jerk
7.8 Linkages of N Bars
7.9 Reference
7.10 Problems
7.11 Virtual Laboratory
……
Chapter 8 Cam Design
Chapter 9 Gear Trains
PART Ⅱ DYNAMICS OF MACHINERY
Appendices
文摘
版权页:
插图:
Figure 3—17b* (p.126) shows a "fleshed out" linkage drawn on top of the H&N atlas page to illustrate its relationship to the atlas information.The double circles in Figure 3—17a (p.126) define the fixed pivots.The crank is always of unit length.The ratios of the other link lengths to the crank are given on each page.The actual link lengths can be scaled up or down to suit your package constraints and this will affect the size but not the shape of the coupler curve.Any one of the ten coupler points shown can be used by incorporating it into a triangular coupler link.The location of the chosen coupler point can be scaled from the atlas and is defined within the coupler by the position vector R whose constant angle φ is measured with respect to the line of centers of the coupler.The H&N coupler curves are shown as dashed lines.Each dash station represents five degrees of crank rotation.So, for an assumed constant crank velocity, the dash spacing is proportional to path velocity.The changes in velocity and the quick—return nature of the coupler path motion can be clearly seen from the clash spacing.
ISBN | 9787111564300 |
---|---|
出版社 | 机械工业出版社 |
作者 | 罗伯特.诺顿 (Robert L.Norton) |
尺寸 | 16 |