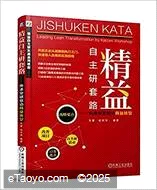
编辑推荐
精益自主研活动的关键流程和操作要领,快速导入改善的实践指南,适合企业、培训公司做培训教程。
开启企业从战略到执行之门,快速导入改善的实践指南
洞察企业商业绩效突破的秘密
领略5日改善的神奇力量
打破部门藩篱发展组织共同解决问题之道
15张表单和10个案例手把手教你做改善。
自主研活动的关键流程和操作要领
精益自主研是一种思想,逻辑而有序的突破;
精益自主研是一种方法,结构化的5日改善;
精益自主研是一种活动,跨职能团队协同并进;
精益自主研是一种育人策略,始于战略终于现场,强调结果关注过程
作者简介
王奎,精益变革管理专家,系统化精益转型方法奠基者,曾历任美国及瑞士咨询公司顾问总监,……,唐道述管理咨询执行董事。王奎先生及他的团队长期服务的企业有:GE通用药业,飞利浦及供应商,通用汽车及核心供应商,上海大众汽车及附属企业,保利协鑫及下属企业,许继集团及下属企业,上航工业集团,徐工集团及下属企业,海尔洗衣机,伊利冷饮,天正电气,菲尼克斯电气等。王奎先生受自主研协会及机械工业出版社之托与俞世洋会长联合编著此书籍,望能为企业提供从精益战略到执行的实施路径与指南。
俞世洋,中国知名精益管理专家,精益类热销书籍《人本精益》作者,精益自主研应用套路的开发者。俞世洋先生拥有二十年制造业工作经历,曾领导过大型企业集团进行系统的精益转型变革。在精益运营、精益财务、精益教练、精益体系建设等领域均拥有丰富的理论研究与实践经验。历任上市公司COO、公司总经理,精益自主研协会会长,精益咨询业独立项目监理人。俞世洋先生于2011年创立精益自主研协会,目前协会拥有会员近万人,已成为中国颇具影响力的精益社群组织。协会以开放、分享、务实、公益为基本理念,以支持中国精益实践者的成长为使命。协会运营至今,不断整合资源,先后开创并运营:精益自主研系列活动、精益自主研种子发展计划、精益大师弟子班、创意改善大赛、精益读书会、精益生产公益项目辅导等多种形式,近300场公益活动。惠及企业会员近300家、个人会员2万多人次。
目录
目录
导读
自序:源于持续改善
第1章自主研活动与精益转型
1.1精益转型是这个时代赋予的核心命题
……
1.3丰田运营模式的产生与全球化应用的四个阶段
1.4自主研活动开展之前需要洞察的六个核心理念
1.5精益运营模式导入的五阶段法
第2章自主研活动的起源与标准化
2.1自主研的起源及发展
2.2自主研活动的标准化流程与时间规划
2.3自主研活动前四周准备流程的标准化
2.4自主研五日改善活动内容的标准化
2.5自主研活动跟进的标准化
2.6自主研活动的特征与需要遵守的12个基本原则
第3章自主研活动主题的来源
3.1改善战略规划
3.2自主研活动与策略部署
3.3自主研活动与价值流分析
3.4自主研活动与日常运营
第4章自主研活动组织和角色
4.1自主研团队的组织构建
4.2支持领导:团队力量的赋予者并领导团队走向成功
4.3推进者:自主研活动的组织者和协调人,维护活动标准化流程并为活动成功开展提供保障
4.4引导者:帮助团队成功,让改善的光芒在实施者身上闪耀
4.5改善组长:构建有创造力和执行力的团队,带领小组成员走向成功
4.6小组成员:聚沙成塔,凝聚团队的力量取得成果
第5章自主研活动的前期准备
5.1自主研活动申请
5.2自主研准备检查表
5.3团队成员的选择
5.4活动日程表
5.5物品准备清单
5.6沟通计划
精益自主研套路目录第6章自主研活动的实施
6.1自主研活动第一天:启动与培训
6.2自主研活动第二天:观察流程与数据检讨
6.3自主研活动第三天:改善实施与模拟验证
6.4自主研活动第四天:持续优化与标准作业
6.5自主研活动第五天:报告发布并庆祝胜利
6.6自主研活动的评价与反馈
6.7自主研活动过程中的个人发布技巧
第7章自主研活动的实施跟进
7.1自主研后30天跟进——构建“第一轮跟进与支持团队”并实施可视化和责任制
7.2自主研后60天跟进——跨部门培训和跟进计划实施
……
第8章自主研活动的成果保持
8.1日常改善的SDCA是对PDCA改善系统的延伸
8.2构建管理幅度合适的小组团队架构
8.3重启标准作业改善愿景
8.4目视化管理沟通单元
8.5主管标准作业和纸卡系统
附录自主研活动案例及其A3报告
案例1重庆海尔洗衣机老工厂布局设计自主研活动总结
案例2江苏汉资餐饮集团晋家门品牌南京滨润汇店岗位工作标准化自主研活动总结
案例3天正电气配电事业部TGM1线单元线设计自主研活动总结
案例4成都伊利冷饮事业部邛崃工厂巧脆棒线快速清洗自主研活动总结
案例5上海飞奥燃气设备有限公司仓储布局及配送模式优化自主研活动总结
案例6欧玛嘉宝中压开关(昆山)工厂均衡化生产自主研活动总结
案例7徐工集团挖掘机械有限公司中挖装配线标准作业自主研活动总结
案例8登电集团热电公司燃油泵房TPM-AM初期清扫自主研活动总结
案例9南阳飞龙汽车零部件有限公司机加二车间质量改善自主研活动总结
案例10苏州协鑫光伏科技有限公司粘棒车间效率提升自主研活动总结
序言
自序 源于持续改善
“我们所做的,其实就是注意从接到顾客订单到向顾客收款这期间的作业时间,由此消除不能创造价值的浪费,以缩短作业周期。”大野耐一这样描述丰田生产方式的精髓。在实际改善过程中,通过追求产品的流动和削减在制品库存来消除浪费、加速流动。当制程之间能流动时,首选流动;当制程之间无法流动时,建立FIFO(先进先出)通道,确立SWIP(标准在制品)或采用后制程拉动来减少库存。它可以用一个公式来描述:制造提前期(LT)=在制品库存(WIP)×节拍时间(TT)。可见,当在制品库存降低时,制造周期自然缩短。然而,在制品存在的主要原因是制程的换产能力不足、制程的批量限制,以及为不稳定的生产系统和供应商系统准备的安全库存。这些恰恰是现场改善最能发挥价值的主战场。
以现场改善为起点,发展到整个企业的经营战略与管理……。自1990年詹姆斯·沃麦克(James P.Womack)出版《改变世界的机器》一书,将丰田式管理模式正式命名为精益生产以来,这种极具生命力的经营管理模式便被迅速传播、学习和实践。致力于将精益模式的核心思维——消除浪费,应用到自身企业的实践者也都快速获益,在不断积累小的改善成果后获得了战略上的竞争优势。……正呈现出丰硕成果:美国丹纳赫公司自1988年开始推行精益生产,在丰田模式的基础上发展出适合自己业务形态的丹纳赫商业系统(Danaher Business System,DBS),通过不断的业务整合、精益系统的导入和改进,加速流动、减少库存、释放现金流,用释放的现金进行下一轮并购。近30年来,丹纳赫公司营业额、净利润和总资产的复合增速分别达到14.4%、20.5%和16.8%。公司股价更是上涨了9641%(年均达到23.1%),而同期的标普500指数涨幅仅为356%。波音公司在20世纪90年代以来借鉴精益生产的理念和方法,在飞机制造上导入“精益+”的运营理念,2006年启动了飞机的移动装配线,将飞机的移动速度定义为1.6in/min,产线在制品数量由20架减少到8~10架。同年,波音公司导入世界上第一条精益脉动装配线——Apache脉动装配线,装配工时减少85%,也因此获得美国制造业最高奖“新乡奖”。美国铝业公司(ALCOA)始建于1888年,被公认为全球最大的铝业公司,在36个国家和地区有超过个运营机构,在全球共有12.7万名雇员。它通过构建自己的精益运营体系——美铝商业运营系统(Alcoa Business System,ABS)——用于管理各项业务的一套原则和工具的集成系统,以及通过年度策略部署(Policy Deployment,丰田称之为Hoshin Kanri,方针管理)和A3项目改善模式,不断降低成本:1998—2000年节省11亿美元的年度支出;2001—2003年节省成本10.12亿美元;2004—2006年节省12亿美元的年度支出。美国泰德康医疗集团从2002年开始导入精益思想。例如,把缩短治疗时间作为奋斗目标和执行准则,利用价值流图和面条图等工具改善中风患者的治疗时间。经过改善,60min内确诊并使用溶栓治疗的病例由14%提升到50%,死亡率由8.8%降低为7.6%。通过导入精益思想,美国泰德康医疗集团从一家品牌和服务都非常普通的医疗机构变成全美医疗界中质量上乘、服务优良、价格优势明显的医院。
精益自主研套路源于持续改善自序回顾丰田公司举世瞩目的成就、丹纳赫傲人的商业绩效、波音飞机的流动生产模式、美国铝业巨大的成本节约、泰德康医疗集团的优秀服务……无一不让人羡慕不已。我国有句古语说得很好:“临渊羡鱼,不如退而结网。”提炼这些优秀企业的做法,发现它们有一个共同的特点:所有的改善落脚点都是现场流程的变化和改进。这也与精益的思维完全吻合:现场是创造价值的地方,也是最容易产生浪费的地方,当致力于消除从客户订单到交付整个过程中的浪费时,流程就变得精益起来。
精益是结果……。因此,另外一个有着深远影响的概念是“改善”。它的核心思维是通过培育微小而持续的改变,不断地累积,进而行至至臻完美的境界。这种至臻的境界可以用另外一个词汇去描述,即“Dantotsu”,如图0-3所示。这是一个日文词语,意思是“断然的领先,绝对的领先”。很多世界级企业在踏上精益之路的起点时,就拟定了这样一个宏伟的愿景来激励团队,要敢于不断否定现状,不断积累小的进步来获取绝对领先的竞争优势。
图0-3Dantotsu
当企业树立精益运营的愿景时,要立刻梳理的第二个问题便是如何来推进精益。有人说:“懂得如何避免失败,你就成功了。”然而,真正要让企业学会如何避免失败却是一件极不容易的事情。因为精益推进通常是自上而下的活动,它易学难精的特征迷惑了很多人。它的基础哲学体系非常简单:定义客户价值,建立价值流,流动,拉动,尽善尽美。在推进一个新的管理体系时,本身就涉及组织和文化的变革,再加上精益运营模式技术体系的复杂性,很多企业在推进精益的道路上饱经磨难。坚持下来的企业值得尊敬,但丧失了时间成本;放弃的企业也不在少数,只能等待时机再次出发。某著名国际战略咨询公司调查显示,自认为精益推进成功的企业不到15%。为了让更多的企业少走弯路,本书作者根据多年精益咨询的经验,总结出三种常见的精益推进的误区和错误做法,下面分享给读者。
第一种常见的错误做法是重视精益文化,忽略改善技术和工具方法。这种做法在一些大型的集团型企业中尤为常见和突出,各种宣传横幅、海报、杂志、内部公众号等内部媒体处处可见精益的身影,人人谈改善,月月办活动,但真正落实到现场和产品的改善屈指可数。待热情褪去,每个人冷静下来思考精益给企业运营带来的价值时,又不免心生迟疑和困惑。
第二种常见的错误做法是精益工具专家改善型。这种做法常见于自下而上推进精益的企业,推进者从局部视角观察,扮演改善专家的角色主导改善的实施,但没有意识到自己还兼有推进者的职能,没有通过活动或文化建设影响更多的人,也没有让改善的思想逐步遍及企业的每个角落。结果是经过一两年的改善,现场也不断出现亮点,但常常是工具优先而忽略了改善本身问题和目标导向。同时,真正进行改善的人只有主导推进的寥寥几位专家,很多职能部门没有任何改进的意识和活动,更没有上升到公司层面去推进。
还有一种错误做法也较为普遍,即虽然文化建设与改善工具的应用并重,但改善的次序较为随机,没有总体纲领和路线图指引。这种形态也往往同忽略内部专家人才培养的问题并存。这种做法的结果是历经几年的改善仍无法形成企业自身的推进方法和套路,阶段性地产生方向上的迷茫。精益运营系统在一个企业中的萌芽、发展、壮大到成功的导入具有客观规律,也与企业的行业特征和地位以及企业的阶段战略密不可分。企业根据愿景和战略结合自身现状拟定的精益3~5年推进路线图可以给予企业良好的指引,同时辅以精益人才的培养和发展,可以让企业让真正迈上精益运营的道路。
这些错误产生的主要原因是精益改善的导入偏离了实现客户价值这一核心,而实现客户价值的具体手段就是消除浪费,现场改善是最为直接的手段和做法。而改善工具、改善的活动形式、改善的文化、愿景等均是为这一现场改善服务的。只有清楚地明了这个逻辑结构,才不会在精益变革的道路上迷失,也不会在众多的精益改善方法面前不知所措。本书的出版旨在能让所有推进精益改善的企业和机构回归客户价值和现场改善这一核心主题,发展适合自己的改善形态和改善文化。当我们关注并实践现场改善这一主题时,它是工具、方法;当我们有力量让企业的所有人致力于现场改善并力求时,它就是一个伟大的战略。因为在实践持续的现场改善时,对人才的育成,对文化的培养,对塑造企业客户价值导向的优异流程,都有着超乎想象的伟大贡献,丰田公司的辉煌成就也正是基于这样一个起点。
本书具体描述自主研活动的关键流程和操作要领,通过这种“好莱坞模式”的快速改善,希望唤醒读者心中持续改善的热情,能以宏观战略的视角看待改善形态与精益运营模式的构建,让所有具备改善意愿的朋友都能够实践持续改善的具体活动,并见证自主研改善活动所能带来的突破性绩效。这也是作者所期望赋予本书的全部意义。
精益自主研活动的关键流程和操作要领,快速导入改善的实践指南,适合企业、培训公司做培训教程。
开启企业从战略到执行之门,快速导入改善的实践指南
洞察企业商业绩效突破的秘密
领略5日改善的神奇力量
打破部门藩篱发展组织共同解决问题之道
15张表单和10个案例手把手教你做改善。
自主研活动的关键流程和操作要领
精益自主研是一种思想,逻辑而有序的突破;
精益自主研是一种方法,结构化的5日改善;
精益自主研是一种活动,跨职能团队协同并进;
精益自主研是一种育人策略,始于战略终于现场,强调结果关注过程
作者简介
王奎,精益变革管理专家,系统化精益转型方法奠基者,曾历任美国及瑞士咨询公司顾问总监,……,唐道述管理咨询执行董事。王奎先生及他的团队长期服务的企业有:GE通用药业,飞利浦及供应商,通用汽车及核心供应商,上海大众汽车及附属企业,保利协鑫及下属企业,许继集团及下属企业,上航工业集团,徐工集团及下属企业,海尔洗衣机,伊利冷饮,天正电气,菲尼克斯电气等。王奎先生受自主研协会及机械工业出版社之托与俞世洋会长联合编著此书籍,望能为企业提供从精益战略到执行的实施路径与指南。
俞世洋,中国知名精益管理专家,精益类热销书籍《人本精益》作者,精益自主研应用套路的开发者。俞世洋先生拥有二十年制造业工作经历,曾领导过大型企业集团进行系统的精益转型变革。在精益运营、精益财务、精益教练、精益体系建设等领域均拥有丰富的理论研究与实践经验。历任上市公司COO、公司总经理,精益自主研协会会长,精益咨询业独立项目监理人。俞世洋先生于2011年创立精益自主研协会,目前协会拥有会员近万人,已成为中国颇具影响力的精益社群组织。协会以开放、分享、务实、公益为基本理念,以支持中国精益实践者的成长为使命。协会运营至今,不断整合资源,先后开创并运营:精益自主研系列活动、精益自主研种子发展计划、精益大师弟子班、创意改善大赛、精益读书会、精益生产公益项目辅导等多种形式,近300场公益活动。惠及企业会员近300家、个人会员2万多人次。
目录
目录
导读
自序:源于持续改善
第1章自主研活动与精益转型
1.1精益转型是这个时代赋予的核心命题
……
1.3丰田运营模式的产生与全球化应用的四个阶段
1.4自主研活动开展之前需要洞察的六个核心理念
1.5精益运营模式导入的五阶段法
第2章自主研活动的起源与标准化
2.1自主研的起源及发展
2.2自主研活动的标准化流程与时间规划
2.3自主研活动前四周准备流程的标准化
2.4自主研五日改善活动内容的标准化
2.5自主研活动跟进的标准化
2.6自主研活动的特征与需要遵守的12个基本原则
第3章自主研活动主题的来源
3.1改善战略规划
3.2自主研活动与策略部署
3.3自主研活动与价值流分析
3.4自主研活动与日常运营
第4章自主研活动组织和角色
4.1自主研团队的组织构建
4.2支持领导:团队力量的赋予者并领导团队走向成功
4.3推进者:自主研活动的组织者和协调人,维护活动标准化流程并为活动成功开展提供保障
4.4引导者:帮助团队成功,让改善的光芒在实施者身上闪耀
4.5改善组长:构建有创造力和执行力的团队,带领小组成员走向成功
4.6小组成员:聚沙成塔,凝聚团队的力量取得成果
第5章自主研活动的前期准备
5.1自主研活动申请
5.2自主研准备检查表
5.3团队成员的选择
5.4活动日程表
5.5物品准备清单
5.6沟通计划
精益自主研套路目录第6章自主研活动的实施
6.1自主研活动第一天:启动与培训
6.2自主研活动第二天:观察流程与数据检讨
6.3自主研活动第三天:改善实施与模拟验证
6.4自主研活动第四天:持续优化与标准作业
6.5自主研活动第五天:报告发布并庆祝胜利
6.6自主研活动的评价与反馈
6.7自主研活动过程中的个人发布技巧
第7章自主研活动的实施跟进
7.1自主研后30天跟进——构建“第一轮跟进与支持团队”并实施可视化和责任制
7.2自主研后60天跟进——跨部门培训和跟进计划实施
……
第8章自主研活动的成果保持
8.1日常改善的SDCA是对PDCA改善系统的延伸
8.2构建管理幅度合适的小组团队架构
8.3重启标准作业改善愿景
8.4目视化管理沟通单元
8.5主管标准作业和纸卡系统
附录自主研活动案例及其A3报告
案例1重庆海尔洗衣机老工厂布局设计自主研活动总结
案例2江苏汉资餐饮集团晋家门品牌南京滨润汇店岗位工作标准化自主研活动总结
案例3天正电气配电事业部TGM1线单元线设计自主研活动总结
案例4成都伊利冷饮事业部邛崃工厂巧脆棒线快速清洗自主研活动总结
案例5上海飞奥燃气设备有限公司仓储布局及配送模式优化自主研活动总结
案例6欧玛嘉宝中压开关(昆山)工厂均衡化生产自主研活动总结
案例7徐工集团挖掘机械有限公司中挖装配线标准作业自主研活动总结
案例8登电集团热电公司燃油泵房TPM-AM初期清扫自主研活动总结
案例9南阳飞龙汽车零部件有限公司机加二车间质量改善自主研活动总结
案例10苏州协鑫光伏科技有限公司粘棒车间效率提升自主研活动总结
序言
自序 源于持续改善
“我们所做的,其实就是注意从接到顾客订单到向顾客收款这期间的作业时间,由此消除不能创造价值的浪费,以缩短作业周期。”大野耐一这样描述丰田生产方式的精髓。在实际改善过程中,通过追求产品的流动和削减在制品库存来消除浪费、加速流动。当制程之间能流动时,首选流动;当制程之间无法流动时,建立FIFO(先进先出)通道,确立SWIP(标准在制品)或采用后制程拉动来减少库存。它可以用一个公式来描述:制造提前期(LT)=在制品库存(WIP)×节拍时间(TT)。可见,当在制品库存降低时,制造周期自然缩短。然而,在制品存在的主要原因是制程的换产能力不足、制程的批量限制,以及为不稳定的生产系统和供应商系统准备的安全库存。这些恰恰是现场改善最能发挥价值的主战场。
以现场改善为起点,发展到整个企业的经营战略与管理……。自1990年詹姆斯·沃麦克(James P.Womack)出版《改变世界的机器》一书,将丰田式管理模式正式命名为精益生产以来,这种极具生命力的经营管理模式便被迅速传播、学习和实践。致力于将精益模式的核心思维——消除浪费,应用到自身企业的实践者也都快速获益,在不断积累小的改善成果后获得了战略上的竞争优势。……正呈现出丰硕成果:美国丹纳赫公司自1988年开始推行精益生产,在丰田模式的基础上发展出适合自己业务形态的丹纳赫商业系统(Danaher Business System,DBS),通过不断的业务整合、精益系统的导入和改进,加速流动、减少库存、释放现金流,用释放的现金进行下一轮并购。近30年来,丹纳赫公司营业额、净利润和总资产的复合增速分别达到14.4%、20.5%和16.8%。公司股价更是上涨了9641%(年均达到23.1%),而同期的标普500指数涨幅仅为356%。波音公司在20世纪90年代以来借鉴精益生产的理念和方法,在飞机制造上导入“精益+”的运营理念,2006年启动了飞机的移动装配线,将飞机的移动速度定义为1.6in/min,产线在制品数量由20架减少到8~10架。同年,波音公司导入世界上第一条精益脉动装配线——Apache脉动装配线,装配工时减少85%,也因此获得美国制造业最高奖“新乡奖”。美国铝业公司(ALCOA)始建于1888年,被公认为全球最大的铝业公司,在36个国家和地区有超过个运营机构,在全球共有12.7万名雇员。它通过构建自己的精益运营体系——美铝商业运营系统(Alcoa Business System,ABS)——用于管理各项业务的一套原则和工具的集成系统,以及通过年度策略部署(Policy Deployment,丰田称之为Hoshin Kanri,方针管理)和A3项目改善模式,不断降低成本:1998—2000年节省11亿美元的年度支出;2001—2003年节省成本10.12亿美元;2004—2006年节省12亿美元的年度支出。美国泰德康医疗集团从2002年开始导入精益思想。例如,把缩短治疗时间作为奋斗目标和执行准则,利用价值流图和面条图等工具改善中风患者的治疗时间。经过改善,60min内确诊并使用溶栓治疗的病例由14%提升到50%,死亡率由8.8%降低为7.6%。通过导入精益思想,美国泰德康医疗集团从一家品牌和服务都非常普通的医疗机构变成全美医疗界中质量上乘、服务优良、价格优势明显的医院。
精益自主研套路源于持续改善自序回顾丰田公司举世瞩目的成就、丹纳赫傲人的商业绩效、波音飞机的流动生产模式、美国铝业巨大的成本节约、泰德康医疗集团的优秀服务……无一不让人羡慕不已。我国有句古语说得很好:“临渊羡鱼,不如退而结网。”提炼这些优秀企业的做法,发现它们有一个共同的特点:所有的改善落脚点都是现场流程的变化和改进。这也与精益的思维完全吻合:现场是创造价值的地方,也是最容易产生浪费的地方,当致力于消除从客户订单到交付整个过程中的浪费时,流程就变得精益起来。
精益是结果……。因此,另外一个有着深远影响的概念是“改善”。它的核心思维是通过培育微小而持续的改变,不断地累积,进而行至至臻完美的境界。这种至臻的境界可以用另外一个词汇去描述,即“Dantotsu”,如图0-3所示。这是一个日文词语,意思是“断然的领先,绝对的领先”。很多世界级企业在踏上精益之路的起点时,就拟定了这样一个宏伟的愿景来激励团队,要敢于不断否定现状,不断积累小的进步来获取绝对领先的竞争优势。
图0-3Dantotsu
当企业树立精益运营的愿景时,要立刻梳理的第二个问题便是如何来推进精益。有人说:“懂得如何避免失败,你就成功了。”然而,真正要让企业学会如何避免失败却是一件极不容易的事情。因为精益推进通常是自上而下的活动,它易学难精的特征迷惑了很多人。它的基础哲学体系非常简单:定义客户价值,建立价值流,流动,拉动,尽善尽美。在推进一个新的管理体系时,本身就涉及组织和文化的变革,再加上精益运营模式技术体系的复杂性,很多企业在推进精益的道路上饱经磨难。坚持下来的企业值得尊敬,但丧失了时间成本;放弃的企业也不在少数,只能等待时机再次出发。某著名国际战略咨询公司调查显示,自认为精益推进成功的企业不到15%。为了让更多的企业少走弯路,本书作者根据多年精益咨询的经验,总结出三种常见的精益推进的误区和错误做法,下面分享给读者。
第一种常见的错误做法是重视精益文化,忽略改善技术和工具方法。这种做法在一些大型的集团型企业中尤为常见和突出,各种宣传横幅、海报、杂志、内部公众号等内部媒体处处可见精益的身影,人人谈改善,月月办活动,但真正落实到现场和产品的改善屈指可数。待热情褪去,每个人冷静下来思考精益给企业运营带来的价值时,又不免心生迟疑和困惑。
第二种常见的错误做法是精益工具专家改善型。这种做法常见于自下而上推进精益的企业,推进者从局部视角观察,扮演改善专家的角色主导改善的实施,但没有意识到自己还兼有推进者的职能,没有通过活动或文化建设影响更多的人,也没有让改善的思想逐步遍及企业的每个角落。结果是经过一两年的改善,现场也不断出现亮点,但常常是工具优先而忽略了改善本身问题和目标导向。同时,真正进行改善的人只有主导推进的寥寥几位专家,很多职能部门没有任何改进的意识和活动,更没有上升到公司层面去推进。
还有一种错误做法也较为普遍,即虽然文化建设与改善工具的应用并重,但改善的次序较为随机,没有总体纲领和路线图指引。这种形态也往往同忽略内部专家人才培养的问题并存。这种做法的结果是历经几年的改善仍无法形成企业自身的推进方法和套路,阶段性地产生方向上的迷茫。精益运营系统在一个企业中的萌芽、发展、壮大到成功的导入具有客观规律,也与企业的行业特征和地位以及企业的阶段战略密不可分。企业根据愿景和战略结合自身现状拟定的精益3~5年推进路线图可以给予企业良好的指引,同时辅以精益人才的培养和发展,可以让企业让真正迈上精益运营的道路。
这些错误产生的主要原因是精益改善的导入偏离了实现客户价值这一核心,而实现客户价值的具体手段就是消除浪费,现场改善是最为直接的手段和做法。而改善工具、改善的活动形式、改善的文化、愿景等均是为这一现场改善服务的。只有清楚地明了这个逻辑结构,才不会在精益变革的道路上迷失,也不会在众多的精益改善方法面前不知所措。本书的出版旨在能让所有推进精益改善的企业和机构回归客户价值和现场改善这一核心主题,发展适合自己的改善形态和改善文化。当我们关注并实践现场改善这一主题时,它是工具、方法;当我们有力量让企业的所有人致力于现场改善并力求时,它就是一个伟大的战略。因为在实践持续的现场改善时,对人才的育成,对文化的培养,对塑造企业客户价值导向的优异流程,都有着超乎想象的伟大贡献,丰田公司的辉煌成就也正是基于这样一个起点。
本书具体描述自主研活动的关键流程和操作要领,通过这种“好莱坞模式”的快速改善,希望唤醒读者心中持续改善的热情,能以宏观战略的视角看待改善形态与精益运营模式的构建,让所有具备改善意愿的朋友都能够实践持续改善的具体活动,并见证自主研改善活动所能带来的突破性绩效。这也是作者所期望赋予本书的全部意义。
ISBN | 9787111604594 |
---|---|
出版社 | 机械工业出版社 |
作者 | 王奎 |
尺寸 | 16 |